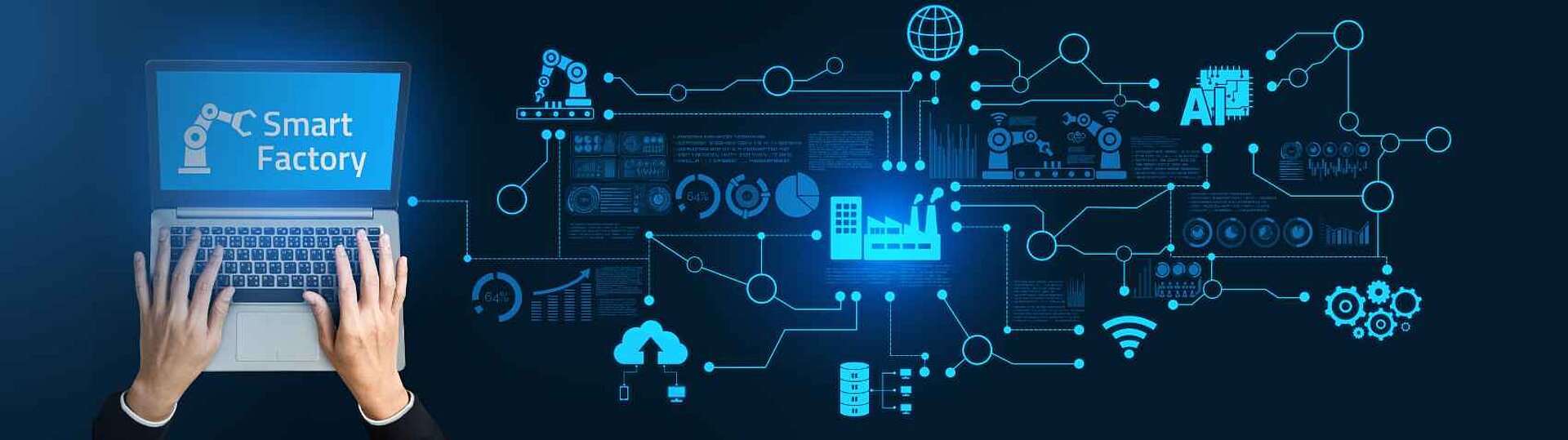
Find out how you can digitalize your production
with solutions from MPDV!
Digital Twin – Smart Factory Glossary
The digital twin is a virtual image of a real device, a machine of a complete line, or even a single process. The digital twin embodies selected features and conditions of the replicated product and is connected to the real object. All known and relevant information such as sensor or machine data is utilized, and the real twin exchanges the data with the digital one.
Machines and objects can be monitored reliably and systematically. You can even simulate different real-life scenarios with the digital twin and make predictions of machine behavior, optimize its operation, or detect anomalies.
Characteristics of the digital twin
From the shop floor scheduling to health management and from virtual training worlds to complex simulation models, the digital twin is advancing. For the digital twin to make full use of all its talents, the following conditions must be met:
- Detailed replication, also based on condition data and sensor values
- Representation of real behavior and simulation of potential behavior
- Continuous exchange between the physical and digital twin
- Comparison and well-designed synchronization of several digital twins
- Tamper-proof implementation, controlled access, and maximum availability
Standardized interfaces are required to ensure that all systems are networked and for an unobstructed data exchange At the same time they transfer control commands from the digital twin to the real system.
Benefits of the digital twin
If real data is combined with variable parameter, real-life simulations are possible. Especially in product development, adaptations of the digital twin can be made much faster than creating physical prototypes, which is a real advantage in product design as time and costs are saved.
If the complete production with all its machines and lines is monitored, even the smallest deviations in the production process can be identified in no time at all. For example, as soon as a temperature value deviates from the norm, the digital twin simulates various scenarios to show the effects. Problems are detected before they arise.
The digital twin makes processes
- faster,
- less expensive,
more effective.
The digital twin in production
In manufacturing, the digital twin is an essential component part of the Smart Factory. Comprehensive data of production resources provide the basis to automate and control processes. Information on machines, tools, materials, NC programs, production resources and tools, product quality, and energy data must be recorded comprehensively and consistently in real time. To create an image that is both realistic and complete, the digital twin contains not only the current data but also historical data.
- Predictive Maintenance: Based on data collected, the software can predict the perfect time for the maintenance of machinery and equipment, which reduces the risk of disruptions and machine downtime.
- Supply chain modeling / material flow planning: The digital twin can use the database to simulate supply bottlenecks or quality problems of raw materials and calculate the best possible alternative scenarios.
- Plan and monitor factory lines: Data from different lines is visualized and a virtual shop floor scheduling is created. For this purpose, machine and production data from the MES, planning data from the ERP, and also process and HR data are utilized.
- Optimize production processes: The digital twin detects and visualizes deficiencies so that countermeasures can be taken swiftly.
- Anomaly detection: When combined with machine learning, the digital twin can identify deviations from the norm fast and reliably.
Further application fields and use cases
The digital twin is versatile and can used be across many areas. Besides the manufacturing industry, the digital twin is used in healthcare, the construction of vehicles, and white goods. It is also a feature in the training and education sector.
- Healthcare: A virtual image of the human body or specific organs can be used to simulate the reaction to drugs. In addition, surgeons can accurately plan complicated procedures on the digital model to assess the chances of success. Similar to the visual shop floor scheduling, a control station in hospitals monitor an entire ward. For this purpose, the digital twin applies health and administrative data.
- Vehicle construction: Engineers can calculate the physical characteristics of a car and simulate driver events with the digital twin.
- White goods: A simple example here is the digital image of a coffee machine that indicates an upcoming change of the water filter. It becomes more complex for portafilter machines where the digital twin has to optimize all subsystems.
- Training: Virtual learning modules simulate the behavior of complex machines. Operators learn how to use them in a three-dimensional, interactive, firsthand, and safe way. This is a decisive advantage, especially for lines with a high hazard potential.
The Manufacturing Integration Platform (MIP)
The Manufacturing Integration Platform by MPDV provides the living space for the digital twin of manufacturing. The integration platform's Virtual Production Reality (ViPR) ensures that all digital twins are stored and can be accessed by applications from different providers. As a result, the MIP acts as the operating system of the Smart Factory and allows seamless interaction between applications, systems and services.
Would you like more information? We are happy to help.
Just fill in the form below. We will take care of your inquiry promptly.