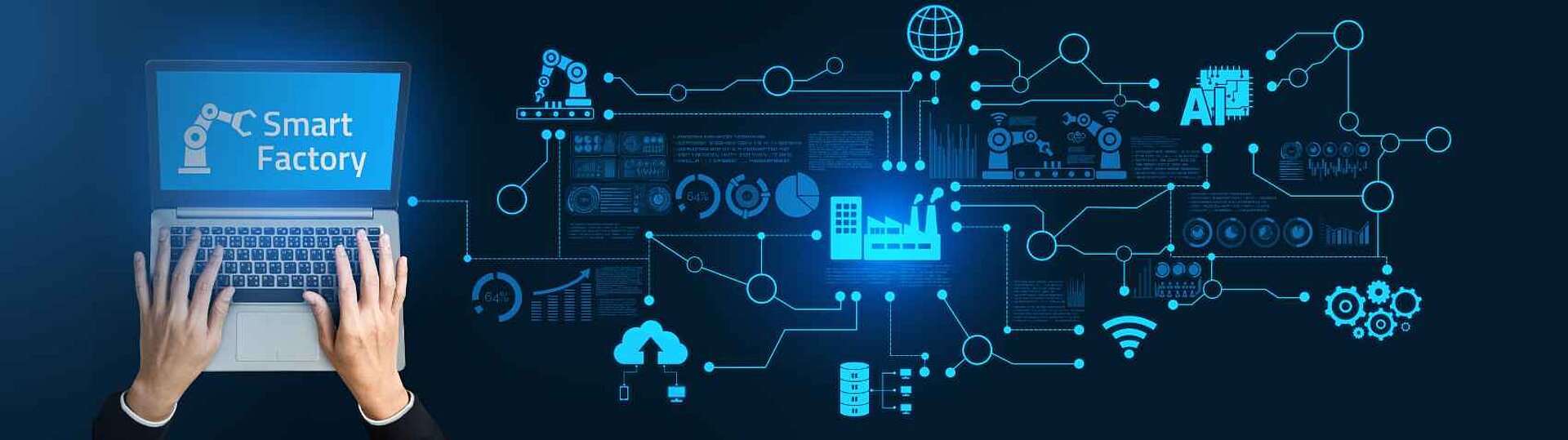
Find out how you can digitalize your production
with solutions from MPDV!
Lean Management – Smart Factory Glossary
Lean management is a comprehensive management approach that aims to optimize processes throughout the company, eliminate waste, and maximize value for the customer. The approach originated in the automotive industry but is now used across all sectors to increase efficiency and competitiveness.
Objectives of lean management
The main objectives of lean management are to make processes in companies leaner, more efficient, and more flexible. By consistently avoiding waste, resources are used more efficiently, and product quality is increased. The lean management approach typically defines seven types of waste, which includes unnecessary waiting times, redundant production steps, or excessive inventories. At the same time, the approach puts the customer at the center: lean management ensures that products and services are provided with minimal effort and maximum value.
Advantages of lean management
The application of lean principles brings numerous advantages:
- Cost savings: More efficient processes reduce material and labor costs.
- Increased productivity: Waste-free processes lead to greater efficiency in production and administration.
- Higher quality: Clear processes and continuous improvements minimize errors and increase product quality.
- Flexibility and faster response times: Companies can adapt more quickly to changing market conditions.
- Employee motivation: Lean, structured processes and employee involvement increase job satisfaction.
5 basic principles of lean management
Lean management optimizes processes, eliminates waste, and increases efficiency.
These five principles help:
- Create value: Consistently align all activities with customer benefit.
- Identify the value stream: Analyze and optimize the entire process to eliminate waste.
- Ensure flow: Design processes so that they function without bottlenecks or interruptions.
- Demand-driven (pull): Production and delivery only take place in response to actual customer demand. This is the way to avoid excess production.
- Strive for perfection: Continuously improving processes to maximize efficiency and quality
The Executive Manufacturing Center (EMC) by MPDV supports companies in successfully implementing lean management, thereby making processes more efficient and reducing waste.
Development of lean management
The origins of lean management can be found in the Toyota Production System (TPS), which was developed by Taiichi Ohno and Shigeo Shingo in the 1950s. The aim was to achieve efficient, customer-oriented production with the fewest possible resources. In the 1990s, the term "lean management" was made popular by the publication of the book “The Machine That Changed the World” and has since become established worldwide as a proven management method.
Sources
- Lean Manufacturing: Wikipedia, 26.02.2025 [online] https://en.wikipedia.org/wiki/Lean_manufacturing (as of 03.03.2025).
- The Machine That Changed the World (book): Wikipedia, 06.01.2025 [online] https://en.wikipedia.org/wiki/The_Machine_That_Changed_the_World_(book) (as of 18.02.2025)
Would you like more information? We are happy to help.
Just fill in the form below. We will take care of your inquiry promptly.