
MES for the plastic production
Many products that we encounter in everyday life are made of plastic – some of them are simple to produce and others more complex. Plastic parts that perform more or less functional tasks can also be found in larger constructions. In most cases, high demands are placed on plastic parts in terms of quality and manufacturing costs. Most of the time, production comes with large piece numbers. This means that efficiency and stable processes are of the utmost importance in plastics processing.
HYDRA X is a Manufacturing Execution System (MES) for all sectors of industry, which offers all essential functions expected in an MES industry solution for plastic production. Companies in the plastics industry also need functions for recording and evaluating data for production, personnel, and quality. All relevant resources are factored in using different mApps for collecting operating, machine, tool and, process data right through to personnel time recording covering all production stages. An MES for the plastics industry should have a variety of integrated functions and pays special attention to issues that are becoming increasingly important.
In combination with the Advanced Planning and Scheduling System (APS) FEDRA, HYDRA X offers special advantages for companies with multi-stage production that want to include other production areas such as toolmaking, assembly, or metalworking departments in the recording of production, quality, and personnel data.
Plastics processing and its specific demands on...
Transparency and efficiency
- Many tools and molds in plastic production have several cavities so that multiple parts can be injected at the same time. HYDRA X manages all these complex tools including the number of shots and maintenance intervals. As a result, all tools are always available and ready for use.
- Setting production parameters for injection molding machines from all manufacturers (e.g. Arburg, Boy, Engel, Fanuc, KraussMaffei, Wittmann Battenfeld, ...) can be time-consuming and error-prone. MES HYDRA X offers functions to automatically transfer setting data directly to the machine control.
- Material consumption plays a major role in plastic processing. HYDRA X can provide consumption data in real time. HYDRA X manages material stocks that are currently in production (WiP, Work in Process).
- Plastics manufacturers are guzzlers when it comes to energy consumption. With the Energy Management from HYDRA X, you keep your eye on it and you can also correlate energy consumption with orders. HYDRA X calculates KPIs like energy consumption per produced article.
Quality and traceability
- The majority of machines supply a wide range of process data during production, such as screw temperature or injection pressure. This data provides information on how stable the manufacturing process runs and what quality can be expected. HYDRA X can collect and analyze it in correlation with other production data.
- High piece numbers are normal in the plastics industry. All the more important is that the quality of the plastic parts is good, deviations are detected at an early stage, and countermeasures can be taken quickly. HYDRA X supports this endeavor by providing a continuous quality assurance. Based on the recorded process parameters, the system can even predict the quality without the need for express testing. Using a combination of predictive quality, AI-based scrap analysis, and the results from the statistical operator inspection, HYDRA X ensures that production runs like clockwork. HYDRA X can also include cavities in inspections.
- For specific target products, the traceability of the raw material and the tools used is crucial. HYDRA X records all resources involved in the manufacturing process and documents them completely. and thus guarantees traceability at all times.
MES success stories in plastics processing
The following companies rely on MPDV's manufacturing IT:
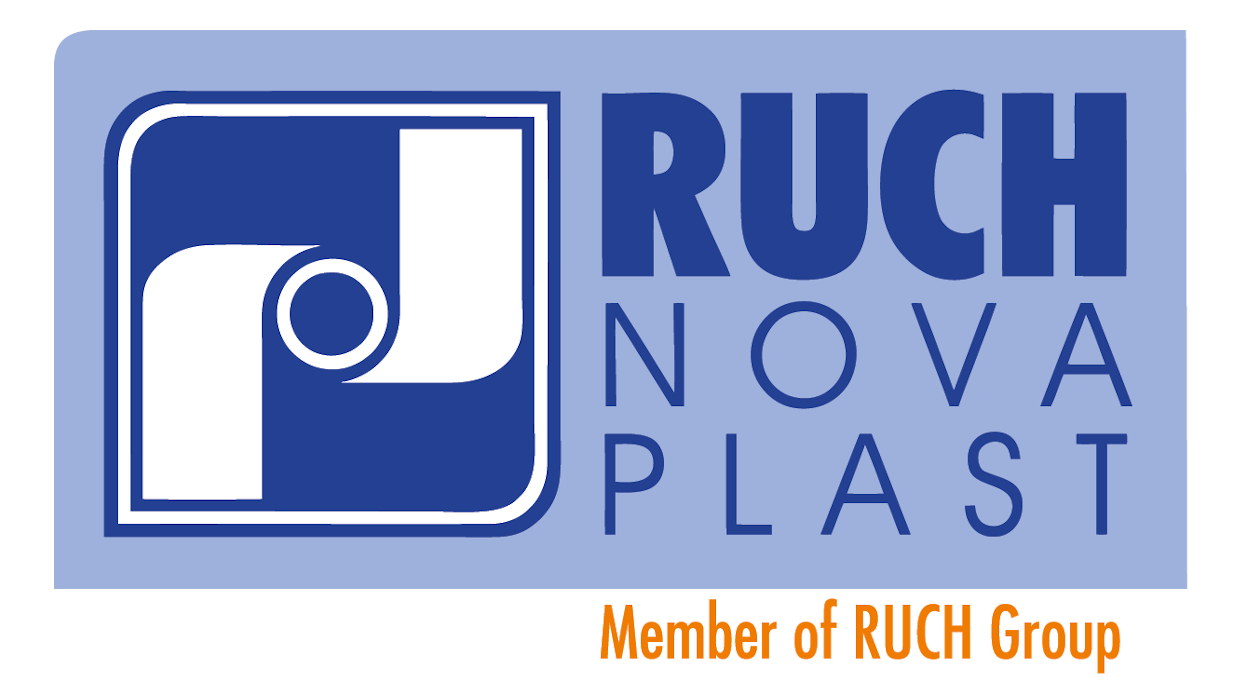
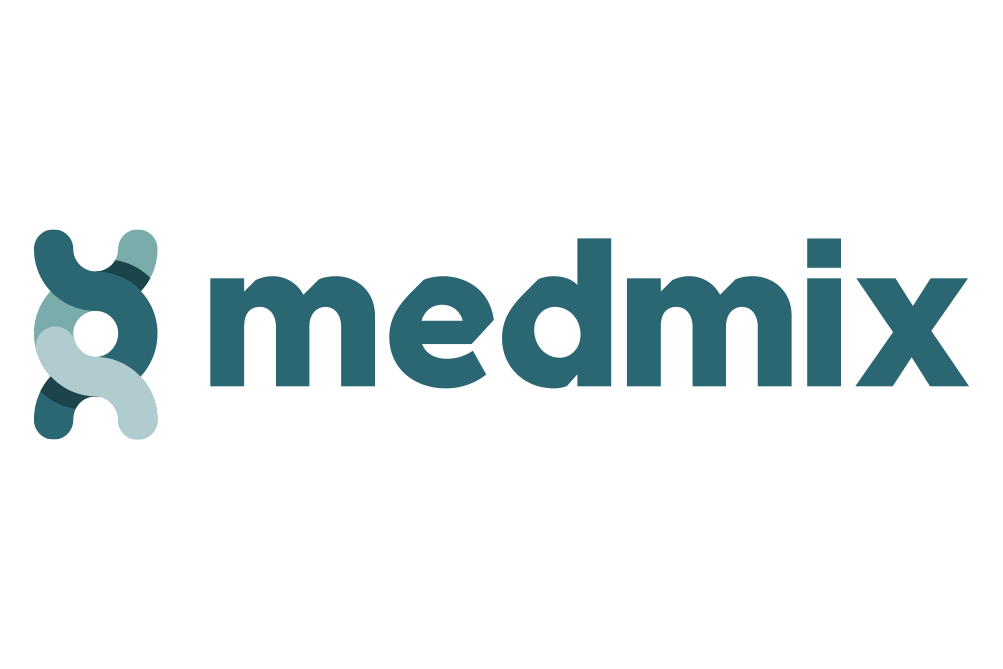
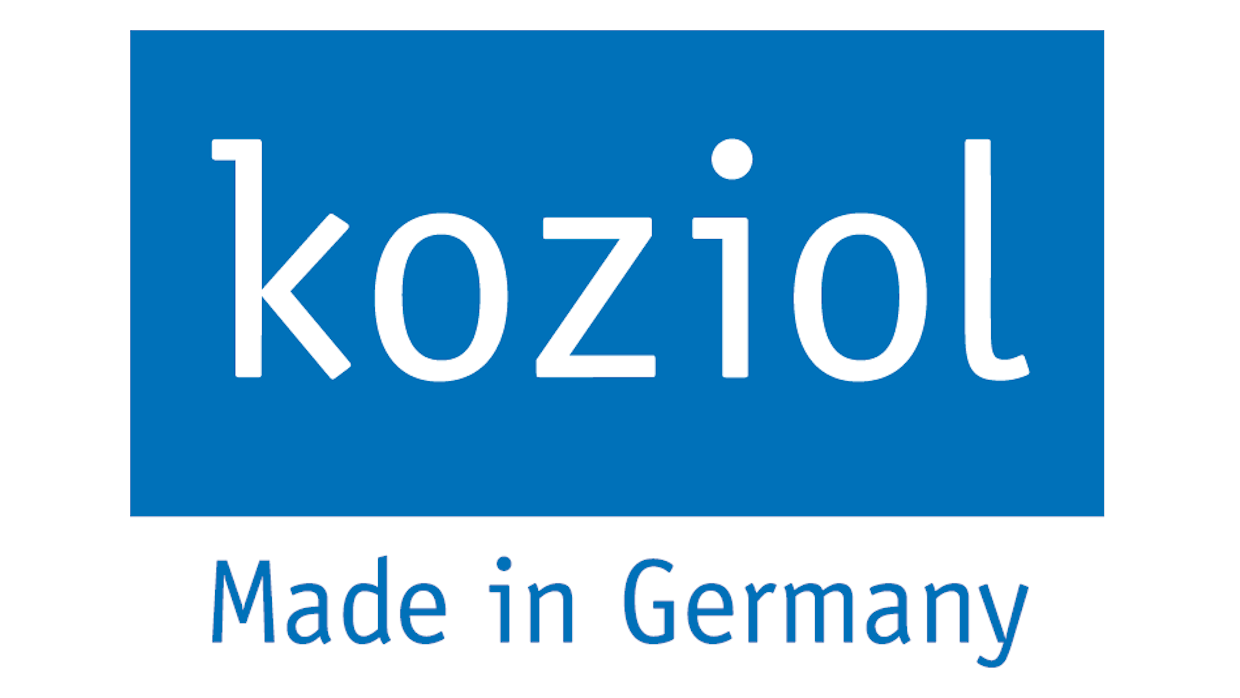
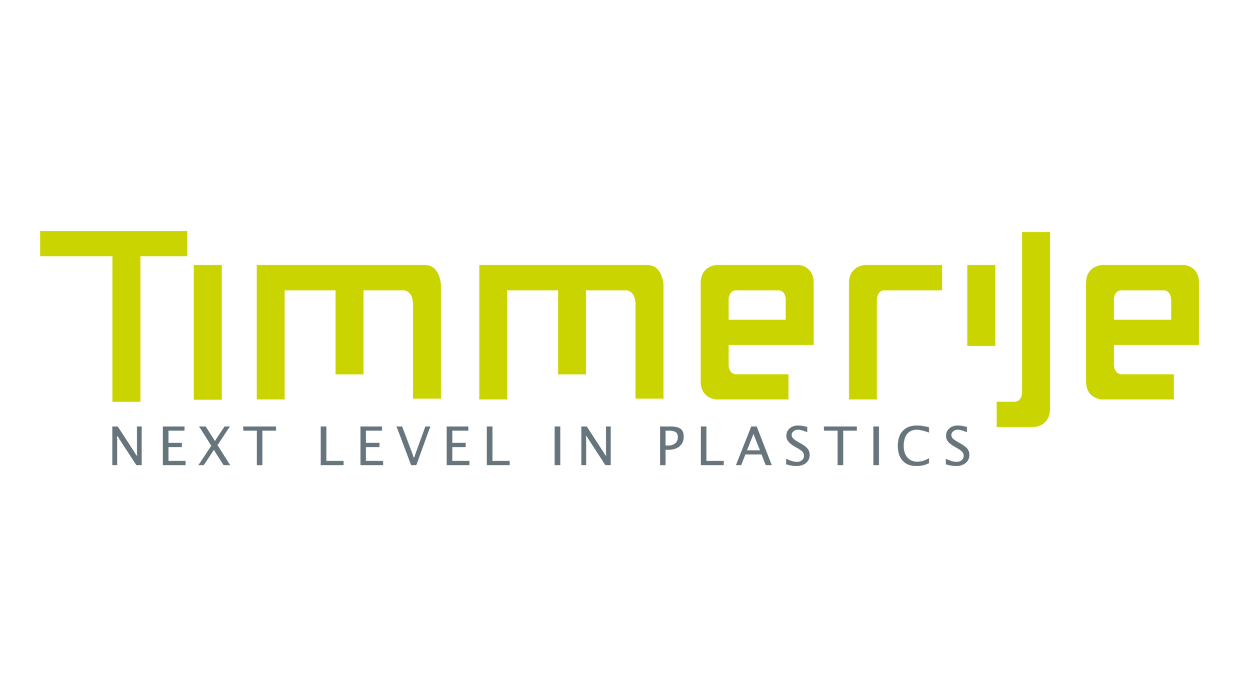
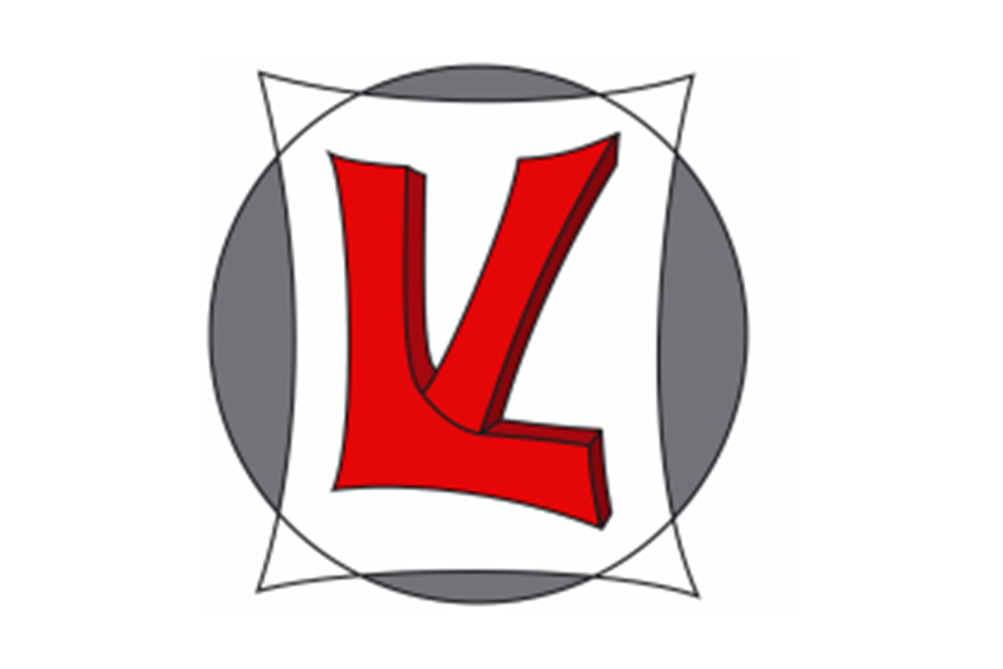
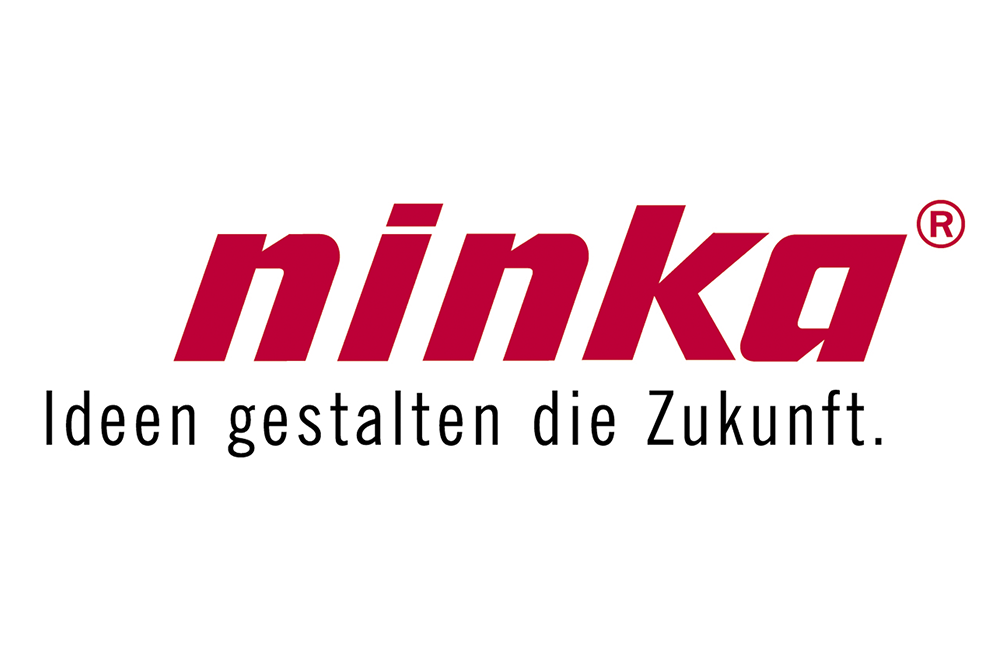
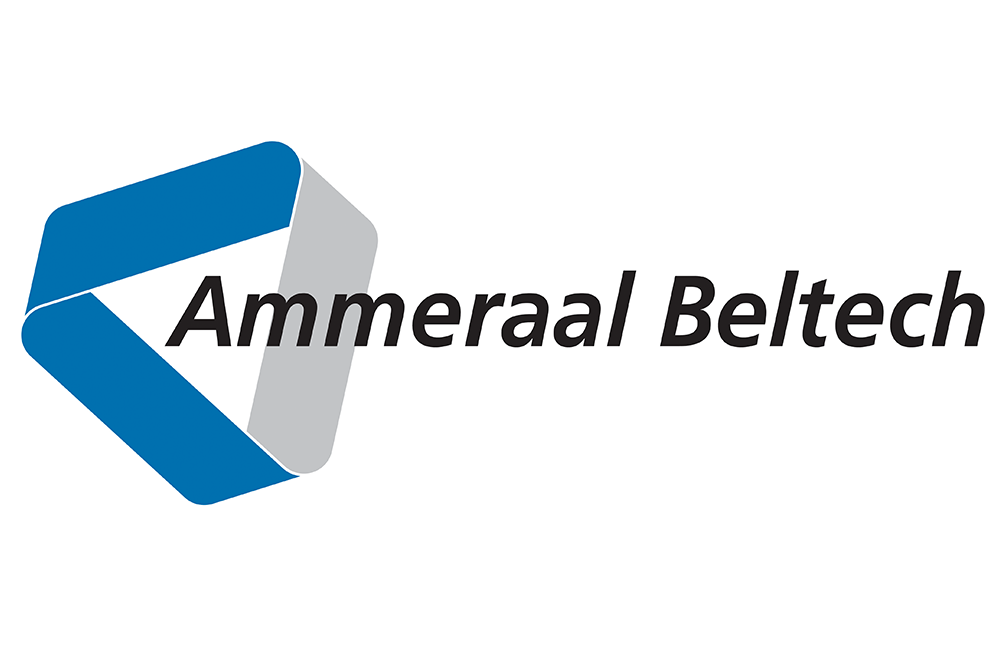
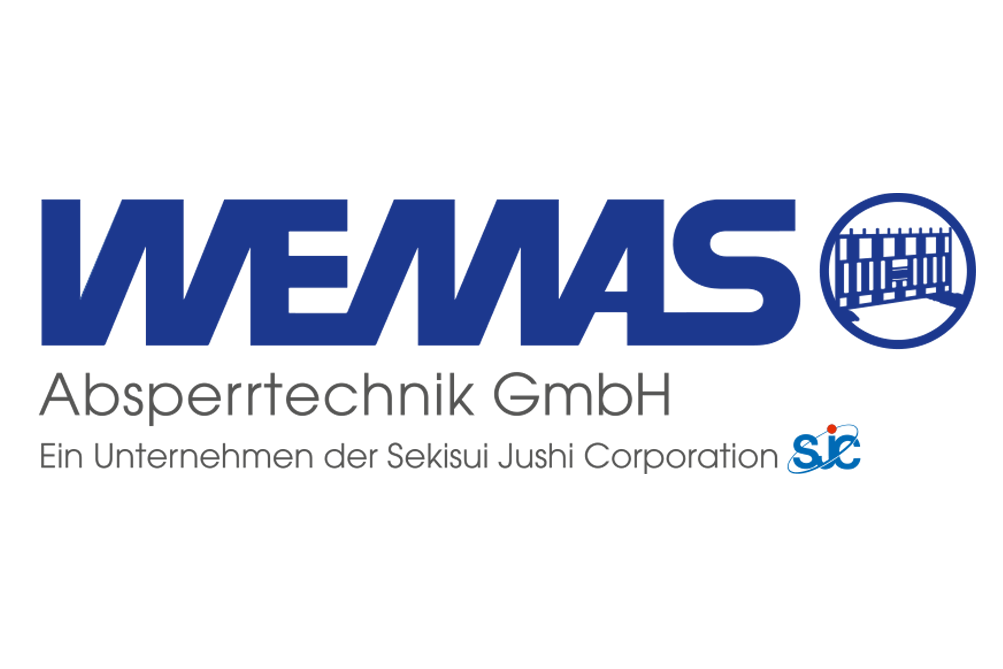